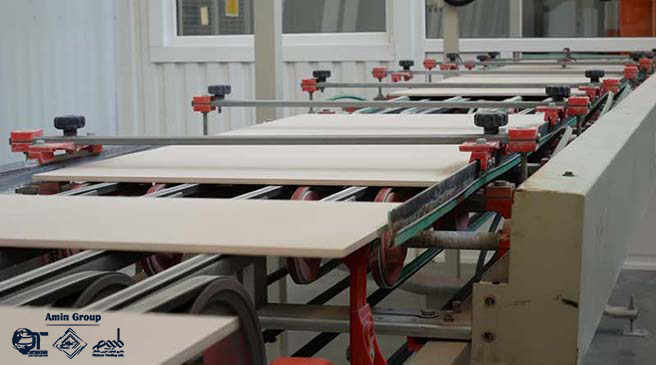
In the old days, ceramic was referred to as a product that was placed in a
hot and dry environment using a slurry of water and soil and was hardened by
the heat of fire. But today, the definition of ceramic is solid objects that
are made of non-metallic minerals and harden with heat.
In the future, stay with Amin Group to explain the production steps of ceramic tiles…
How many types of ceramics do we have?
Ceramics are divided into four categories:
1. Special and technical ceramic products (such as acid-resistant ceramics and tiles)
2. Refractory ceramics
3. Rough ceramic products
4. Fine ceramic products
The ceramic products that are used the most are divided into the following categories:
1. Ceramic household utensils
2. Construction sanitary ceramics
3. The tiles
4. Electrical insulators and insulators
Machines used to produce ceramics and tiles
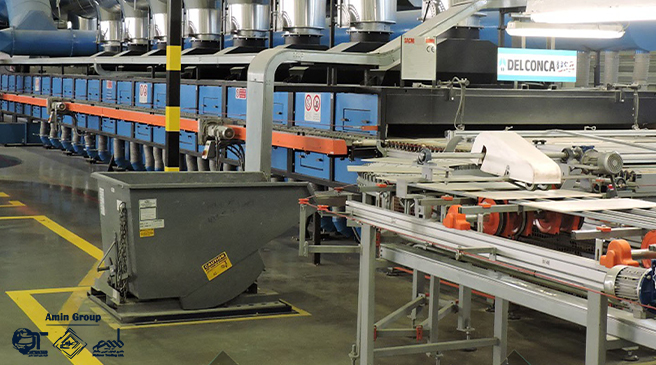
In tile and ceramic factories, they use advanced tools for the production of their products, and these devices are:
“Stone crusher, box feeder, mortar and glaze ball mill, spray dryer, press machine, roller and tunnel furnaces, glaze and decorating line, machines related to packaging and grading”
Production stages of ceramics and tiles in factories
First step: preparing the raw materials needed to make ceramic tiles
The body of tiles is usually taken from different soils in different conditions and from different mines. These tiles and ceramics are made from different raw materials based on their application and role, which are:Plastic raw materials, fillers and melting agents.
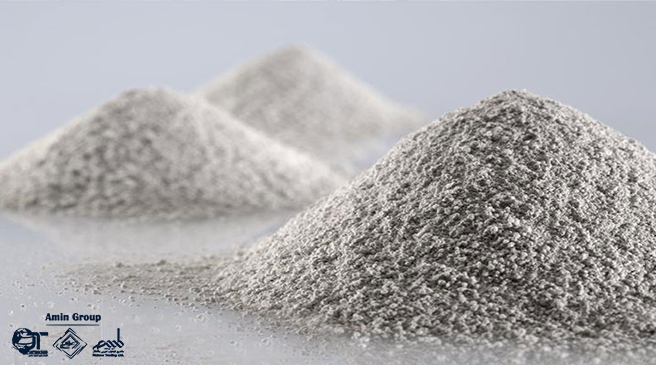
The primary items of plastic mean the plasticity of clay, which is defined as follows: The property of plasticity is the property by which a body can have an elastic state due to pressure and impact. and change its shape without breaking And after removing the pressure or impact, it will return to its original state. One of the characteristics of clay is plasticity.Fillers are non-plastic materials which have high melting temperature and high chemical resistanceand their duty is to prevent the shape of the body from changing during cooking and heating. Also, these items help the glaze to bond with the ceramic itself with a better quality.
Melting agents، They are materials which have a high consumption in ceramics and tile making due to the reduction of the melting point of the body or glaze. These materials melt when heated And when they are cooling They become glassy.The most important body Melting agents used for tiles and ceramics And the most important Melting agents are:Potassium, sodium, calcium and magnesium oxides, which should be supplied with sodium, calcium and potassium feldspars.The next part which is placed in the first stage is the preparation of these raw materialsThe process of these works depends on the type of materials and their size, which we briefly explain below: ü
The first step is to prepare the crushing of hard materials and coarse grainsü which are converted into finer materials by means of a series of stone crushers. ü The next step is grinding For this, ball mills are used.
ü In the mill, in addition to raw materialsü They add some lubricant such as sodium silicate and this causes itü which will gradually turn into a smooth slurry during the work damage of the final mortar.A point that you should keep in mind It is that At each stage, monitoring should be done according to standards.
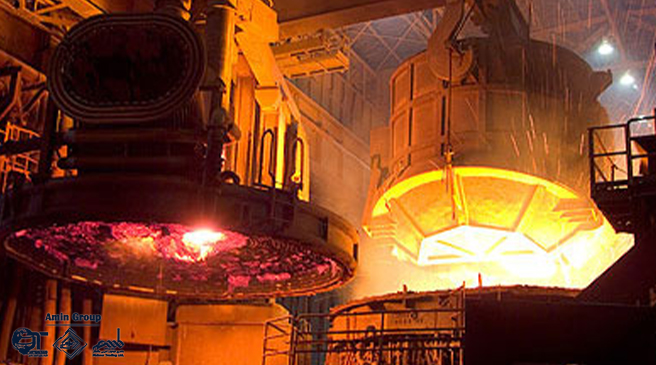
Second step: preparation of powder
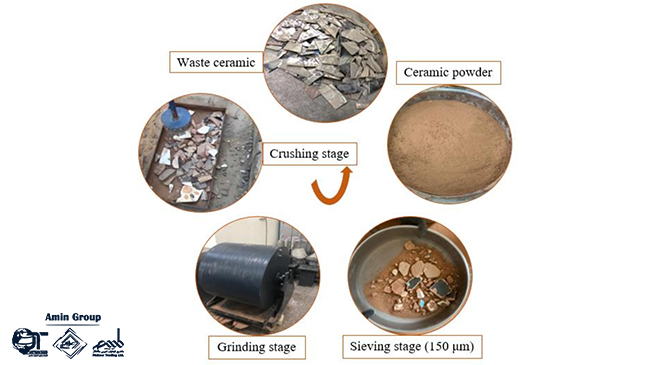
To prepare powder from slurry Spray dryers should be usedThe slurry made in the mills is poured into slurry tanks This topic makes it even will be Then high-pressure pumps pump the slurry to a cylindrical chamber called a spray dryer Deliver
And they spray that slurry in the air, In this place, the slurry meets the hot air and heat and At the end, a soft powder is poured on the conveyor belt under this cylinder. The quality of this powder depends on several factors As:Type of spray nozzles And the number and size of holes and their arrangement ، type of spray dryer, pumping quality and pump pressure, powder moisture and powder granulation, chamber dimensions , the quality of the slurry and the body formula And especially their plasticity and density and viscosity and grout granulation, the temperature inside the chamber, The pressure inside the chamber and the amount of humidity in the chamber, gas pressure stability, powder shelf life, The strength of the powder and the homogeneity of their moisture, The type of nozzles and other nozzle components.
The third step: shaping or pressing the powder
This method is as follows A mixture of raw materials in the form of powder with appropriate granularity It is placed in the cavities of the mold and under pressure And in this way it takes the shape of the mold. In this condition, the moisture in the powder should be around 5%. Today, in tile production industries, There are very modern presses with high capabilities which can even apply the plan in the pressing stage.
The fourth step: Drying ceramics and tiles
In ancient times Drying was done in long tunnels And this would take several days.
This despite the fact that If you use modern dryers You can dry your ceramics after about 20 minutes. Also, drying in the old way caused problems such as cracking and placing ceramics and tiles on top of each other This issue destroys the effect of the work even after glazing. Of course, these problems have been solved by using new devices.
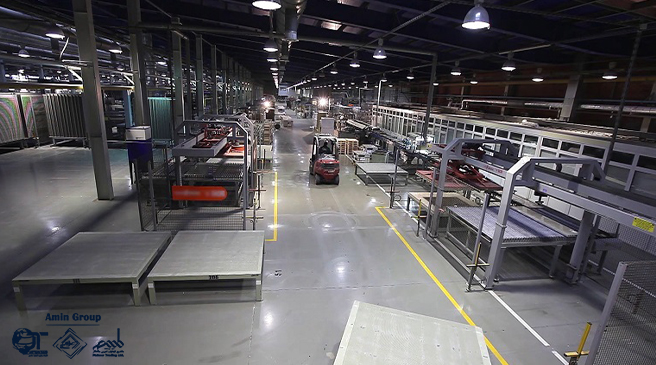
The fifth step: Glazing and appearance corrections
In single firing tiles like the example of Menoproza wall tiles, Porcelain and floor tiles that have glaze After drying the tile, Enter the blue route be And then the lining glaze, which is also called angob It is applied to them And then polishing is done by other devices And the designs in question are done on tiles and ceramics. Of course, it should be said that each color of the print should be done by a separate machine This is related to things like the length of the production line It depends on the drying of tiles and ceramics after each stage of glazing.
New machines used for glazing They are like this which can apply more prints on the tile.Glazing steps are as follows:
– First, they choose the raw materials.
– So, according to the formula that exists for the preparation of glaze Its ingredients are mixed together.
– During wear and grinding
The amount of density is considered for the slurry.
– The material used for glazing is passed through a sieve to find the seeds of a hand.
– They ventilate the glaze to make it last longer.

The sixth step: firing the ceramics and tiles used
After the polishing is done,
It is the turn to bake tiles and ceramics. The basis of tile firing is the time-temperature curvewhich is also called the tile baking curve And this curve is different for different products and tiles with different uses And this curve according to temperatures and thermocouple settings It is considered as existing in the walls or roof of the furnace. Efficiency and efficiency of tile firing depends on thermal energy which is absorbed by the products placed in the oven. If at this stage, not enough attention is paid to the matter of cooking And the principles necessary to do this work are not observed You may encounter problems such as the following:
– Low strength and brittleness
– ransparency and higher brightness levels
– Regarding the terrace and OPEC glazes
– Changing the range of printing and background
– The surface of the glaze is dirty
– The presence of black spots on the glaze
– Glaze hairline cracks and mechanical cracks and fractures and corner jump
– Deformation and warping of tiles and other things related to flatness
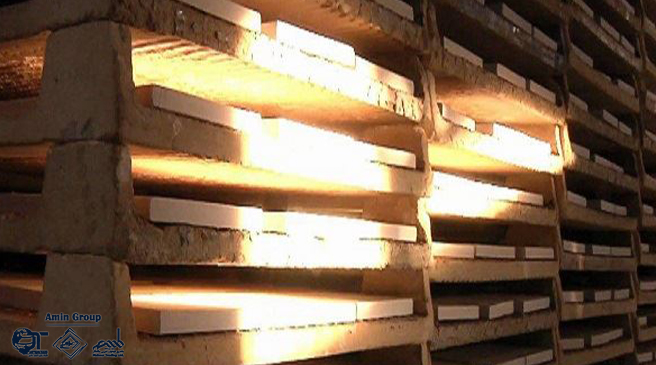
The seventh step: Polishing
This step is only done for unglazed granite tilesGranite tiles are a group of tiles that Their water absorption capacity is less than half percent.When polishing is done There are probably holes on the surface.
This opening reduces the life of ceramic tiles and water penetration.
Amin Group Importer and supplier of tile and ceramic raw materials in Yazd province is with you. Selling all kinds of ceramic tiles to your taste